|
|
|
|
IDEO on Digital Design Tools
by Al Dean
As a technology Editor of a UK-based product development technology magazine, I wanted to find out how those working at the vanguard of product design and development see the role of the digital design systems and technology we cover each month. What started out as a request for answers to a simple question, lead to me speak to some of the most innovative organisations in today's design market. One particularly productive session was held at the London offices of IDEO.
I spent a very interesting hour with three of the staff from IDEO London to discuss how an organisation which works in such a freeform, and at times, seemingly chaotic manner, sees digital design tools fitting into their particular workflow if indeed at all.
It would seem that even the guys at IDEO are a little uncomfortable with the over-use of the term innovation, as Design Engineer, Max Bielenberg commented:
|
|

Max
|
Innovation is a very woolly word. We're supposed to be experts in innovation but even we find it very hard to define. We have a half hour presentation which tries to communicate what innovation is or what it could be. It's a very broad term that is used quite liberally. |

|
|
Industrial Designer, Marc Tanner continued:
|
|

|
Everything that we promote about Innovation has nothing to do with software - ultimately it's a tool. It's about a process and an attitude. On the other hand, we use lots of phrases in that presentation such as iteration, prototyping early, etc. It's clear that there are certain types of design and different parts of the process that CAD tools are pretty good at. For example, helping you iterate quickly and recording the thought process. Just like a pencil and paper is a device for capturing thoughts and moving on, so is Pro/E. That's how it's used here.
|

Marc
|
|
So how do they see the relationship between the tools they use and the end result?
As prototyper, Simon Leach said:
|
|

Simon
|
It's a piece of the toolbox but the tools don't define how we innovate. It's just one of the tools, depending on what the project is and if it's suitable for that particular project, or not." Bielenberg continued:,"It's part of a suite of tools. Part of which is just your brain and your creative thought that you use in the innovation process, which goes from thinking and creating, sketching generally, communicating ideas as fast as you can. That could just be verbally in a brainstorm, it could be pencil sketching, but as it gets more detailed, you have to use more sophisticated tools. 3D CAD is a sophisticated tool that you use further on down the line in the innovation process.
|

|
|
It was interesting to see exactly how this small multi-disciplinary group viewed the role of technology in their work processes clearly they placed as much concentration and emphasis on the use of traditional techniques and methods as they do digital tools, and when 3D CAD is used, it is much further into the design process, where a product's form is much more tightly defined:
|
|
|
The tools that you use in the early part of the innovation are very much a pad, sticky notes, flip charts, foam models, cardboard. There's not much electronic, software-based work, but I think there's a point where you want to record your detailed and sophisticated thoughts.
|

Marc
|

|
|
|

Simon
|
When you start to focus down on some of the ideas and concepts that have come out of a brainstorm or the beginning part of design process, you start to think,'OK, we'll start to explore that one a bit more, or that one a bit more' then you start to print it out and visualize it so your client can really understand what's being spoken about.
|
|

|
|
|
|
Because of what we do, there are other bits of software that we use in the same phase of development. If you're talking 3D CAD, the assumption is that you're talking hard products and we don't just do that. We design interfaces and services, some of which are knobs and buttons, for instance, a car audio product. So where amongst all that lot, there could be some 3D CAD, some Director and Rapid Plus, which are other things we use. They are analogous to Pro/E or SolidWorks in other areas we work. So we tend to tie things together like that, on a really nice full scale project.
|

Marc
|
|
Interestingly, a fact emerged; that the use of CAD at IDEO in the design process is treated with the same value as any other form of model, mock-up or prototype:
|
|

Simon
|
I think it's quite throw away actually. You do one thing does it work? If not, throw it away and start again. I think some people get too precious about the amount of time they've devoted to a Pro/E model. I think this attitude came about when they (the CAD software developers) said you can design, then go to engineering, then straight to manufacturing it's a bit of a fantasy really. So how does CAD data feature in their design to production process, is it really just another form of prototype? ------- You will always start again at the engineering stage because the parameters are slightly different; you need to take different things into consideration from when the industrial design was being done, because they are looking at it from a different perspective, looking at aesthetics. Obviously you take tooling into consideration, but some projects we worked on, we thought 'Can you make it?' Yes, but do we model it with draft? No. We just modelled it so we could make a prototype - and that's it. That data is useful to look at and say,'We can develop on from that', but we probably won't use any of that data again, apart from just to visualize what's already been done and to keep as close to the original design intent as possible. |

|
|
So do they think that a future of 100% digital design is fantasy, or is it still a possibility? This seemed a matter which the team had thought about previously and they weren't short of stories of confused clients and dodgy prototypes. Max Bielenberg recalled a problematic client presentation which illustrates the point perfectly:
|
|

Max
|
In the past I've tried to present a design in a 3D CAD package literally spin a design around in Pro/E. Because we (the designers) are used to looking at that on screen, we understand it, but clients don't. It's actually too big a step for them, it only really works when you make an actual model.
|
|

|
|
|
|
That happened recently. The client couldn't decide if they liked a digital prototype or not, but in the final presentation with a full size, all singing, all dancing model, they were gobsmacked by it. They couldn't envisage it from a flat image but they could from a physical prototype. There was no correlation between the two. Yes, it's a nice picture, but they can't feel it, touch it, they can't see how big it is?
|

Simon
|

|
|
|

Marc
|
We might develop a bezel for the front of a PC monitor. We model what we think the surfaces should be, fiddle with it and try six different ways to build the surfaces to get what we want. Then we stick it on a machine with a block of foam, and suddenly you can see it in real life. I'll be the first to admit that I still get things that come off and think 'bloody hell, that's nowhere near right.' I never really notice it, until I've got it in my hands. ------- At the end of the day, even designers, who rely on their imagination, can only make ultimate judgments when the product in question is sat in front of them, in real-life. These tools have come a long way in making that easier and quicker, but it doesn't change the fact that its slightly throw away.
|
|

|
|
|
|
I think CAD software still underrates the physical prototyping you still need to do. It leads big companies into believing they can do it all digitally but they really need to see, to touch, to understand what's going on at all levels of their new product development process, from the early stages to when they're doing their engineering rigs and stuff.
|

Simon
|

|
|
|

Marc
|
You have to be able to walk around it, you have be able to hold it. You can't make decisions until you've done that. When we're doing block models, there are some great uses for CAD data. There may be pipes, mechanisms, so you can work around them so you're a lot more confident that you're closer to where you should be. But that database just gets thrown away when the model gets made. It will be used by everybody as a reference point but that data will never appear in the final tooling data.
|
|

|
|
|
|
I think we're learning to be less precious about our 3D data. I describe a 3D model as a sketch and often that's all it is.
|

Max
|

|
|
|

Marc
|
The words that people use to describe 3D CAD models give you a clue as to what they think of them. But as soon as somebody else gets it, it's just pure data so they think it must be right.
|
|

|
|
|
|
I think there needs to be some conformity about the language about how you describe it. What the software vendors put out about what this stuff is is very different from what we would eventually class certain levels of what we do as. Clients get all the sales patter, blah, blah, blah. So you're doing something and after having all that talk, they think,'Oh, this is what that is.' ------- In the end it's not final data, it's just what we used to get to this point in time. On the project we're talking about, there wasn't a stage where we said 'We're going to model this in 3D.' We needed a physical model, so what do we need to get it? We did some sketches, some 2D design concepts, chooose a number of them, focus on one, model it up in 3D, stick it on the CNC machine, cut big lumps of foam, paint it, sand it, make it look cool.
|

Simon
|

|
|
|

Marc
|
There are some advantages, in that three people can look at something while you spin it around and talk about it. But again, it's not the fact that the data is there that's important, it's that you can have a conversation about something that has a fair degree of concreteness about it and do all those "what ifs?". Some details you can tweak quite quickly, some you can't, but at least you can do all those "what ifs?" and see what the impact is - relatively quickly. ------- Through that iterative process, that database is carrying a record of those conversations and thoughts. If your machine a piece and it doesn't look right, you don't have to take it and somehow digitize it. It was created digitally, and I have the reference.
|
|

|
|
|
|
It really does reduce the time between when you start with a sketch then say, this is the real thing now. Now, with almost no effort at all, it moves from being a sketch, to unambiguous rock-hard data. That is great! |

Max
|

|
|
|

Marc
|
We used to have a schedule that said there will be two weeks for refining the final design, then two months 'detailing' whatever that meant. Now we have a two month and one week refinement phase, and we'll check there is draft, that the split lines and all the 'details' are in the right place, but suddenly it's off and it's real.
|
|

|
|
|
|
If you start off with and have CAD data, there's obviously a big chain down to manufacturing and you get to that much faster than you did in the past. It gives everybody down that chain a better starting point than they have had before and a chance to hit these tighter deadlines to get a better product to market. That definitely does help.
|

Simon
|

|
|
|

Max
|
It does help getting things right first time, like component clashes and movement of mechanisms within an enclosure. It really does help that a lot.
|
|

|
|
|
|
It makes your iterations a lot more deliberate instead of accidental.
|

Marc
|

|
|
|

Max
|
But there will always be things that you still forget. You can believe that you've checked for component clashes and clashes, but there will always be something that changes a component is modelled out of spec, or there are larger tolerances. Other things you wouldn't have realised until much further down the line, become more apparent in the earlier prototypes.
|
|

|
|
|
|
Design is still a process that happens in people's heads and one that happens between people. Whether that happens in a random, haphazard form in a brainstorm or with someone with ISO9000 processes these are all part of the process which don't refer to CAD or any other kind of software. They are all outside of that.
|

Marc
|
|
It seems that in the end, designers couldn't survive without many of these tools, but of themselves, they don't define the design process. The design process is defined by the people who run it. IDEO and most design groups will tell you how they approach designing things, more often than not, it's not about the tools they use, but the process they go through.
Al Dean
|
|

|
|
|
|
IDEOs top five
Some of the more recent projects that IDEO London has been involved in:
A defibrillator designed for Artema, the Danish medical equipment manufacturer (photo credit: Artema).
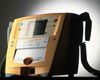
The 2002 Manchester Commonwealth Games Baton (photo credit: Karen Wright).
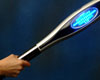
A remotely controlled submarine telepresence vehicle (photo credit: Jason Tozer).
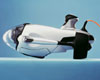
The Palm V connected organiser designed and developed for Palm Computing (photo credit: Steve Moeder).
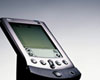
Steelcase Webwizard, a meeting room management display system designed and developed for Steelcase with Appliance Studio (photo credit: Steelcase)
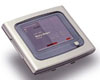
|
|